Машины для уборки зерновых культур. Автономное домолачивающее устройство
Общее устройство комбайна
К атегория:
Комбайны Дон
Общее устройство комбайна
Зерноуборочный комбайн представляет собой сложный агрегат, который служит одновременно для скашивания и обмолота растений, сепарации и очистки зерна и сбора в бункер зерновой фракции. С помощью его выполняют также операции по уборке незерновой части урожая: сбор в копны, укладку в валок или разбрасывание по полю и сбор измельченной соломы в прицепленную к комбайну тележку.
Состав такого агрегата изменяют в зависимости от задач и условий уборки сельскохозяйственных культур.
Основой комбайна считается молотилка, на которой размещены рабочие и транспортирующие органы, бункер с выгрузным устройством, все агрегаты и мосты моторно-ходорой части, гидросистема, рабочее место комбайнера с элементами управления и системой контроля. В нее входят: однобарабанное молотильное устройство, состоящее из бильного барабана и решетчатой деки (подбара-банья), отбойный битер, клавишный сепаратор соломистого вороха (соломотряс), сепаратор зернового вороха (очистка), включающий верхнее и нижнее жалюзийные решета и вентилятор, домолачивающее устройство с молотковым барабаном и глухой декой, транспортирующие устройства (шнеки и элеваторы).
На входе в молотилку шарнирно на опорах скольжения установлена наклонная камера, на которую навешивают жатку сплошного среза, платформу-подборщик или специальные адаптеры для уборки подсолнечника и сои.
Жатвенная часть представляет собой единый агрегат при соединении жатки с наклонной камерой и проставкой. Она опирается на два гидравлических цилиндра, установленных на балке моста ведущих колес. С помощью последних жатвенную часть устанавливают на различной высоте от поверхности поля, поворачивая относительно оси бугелей молотилки.
К основным рабочим органам жатки относят: универсальное мотовило, режущий аппарат, делители, корпус жатки и шнек.
Копнитель снабжен грабельными механизмами (соломонабивателем и половонабивателем) для активного заполнения камеры соломой и половой. На его корпусе шарнирно подвешены дно с пальцами и задний клапан, которые могут открываться по команде оператора из кабины и автоматически - в случае перегрузки камеры.
Ходовая часть комбайна состоит из моста ведущих колес с коробкой диапазонов скоростей и бортовыми редукторами, привода, моста управляемых колес и рулевого устройства с гидравлическим сервоприводом.
Для плавного изменения скорости ведущих колес служат объемный гидропривод (от 0 до 24 км/ч для комбайнов «Дон-1500» и «Дон-1200») и клиноременный вариатор (от 0,6 до 23 км/ч для «Дон-1200»).
Мощность передается на ходовую часть и рабочие органы поликлиновыми ременными передачами с обоих концов коленчатого вала.
Ходовая часть приводится в действие от правого конца коленчатого вала и шкива. Последний установлен с помощью двух шариковых подшипников на специальной опоре и связан с коленчатым валом специальной упругой муфтой - гасителем крутильных колебаний. Шкив привода рабочих органов жестко прикреплен к маховику двигателя за счет промежуточного вала и шлицевого соединения.
Рабочие органы комбайна включаются и выключаются без-муфтным устройством (лениксом). Принцип его работы основан на изменении натяжения приводного ремня плавным перемещением подпружиненного натяжного ролика в диапазоне от нулевого натяжения (леникс выключен) до предельного натяжения во включенном состоянии.
К атегория: - Комбайны Дон
При раздельной уборке потери зерна за валковой жаткой допускаются не более 0,5% для прямостоячих хлебов и 1,5% для полеглых. Потери зерна при подборе валков не должны превышать 1%, чистота зерна в бункере должна быть не менее 96%.
При прямом комбайнировании чистота зерна в бункере должна быть не ниже 95%. За жаткой комбайна допускается до 1% потерь для прямостоячих хлебов и 1,5% для полеглых. Общие потери зерна из-за недомолота и с соломой должны бытьне более 1,5% при уборке зерновых и не более 2% при уборке риса. Дробление не должно превышать 1% для семенного зерна, 2% для продовольственного, 3% для зернобобовых и крупяных культур.
> Назначение и общая характеристика зерноуборочного комбайна «Дон-1500»
Самоходный зерноуборочный комбайн «Дон-1500» предназначен для уборки культур прямым и раздельным комбайнированием во всех зерновых зонах страны с использованием дополнительных приспособлений для уборки зернобобовых, крупяных, мелкосемянных культур, подсолнечника, семенников трав, сои, кукурузы на зерно.
В зависимости от зоны применений и условий уборки комбайн «Дон» можно оборудовать копнителем для сбора соломы и половы или измельчителем с подачей массы в прицепные тележки или разбрасывания ее по полю.
Техническая характеристика
Ширина захвата жатки, м…………………………5; 6; 7; 8,6
Пропускная способность молотилки, кг…………………6-8
Масса с копнителем и 6 метровой жаткой, т…………….13
Ширина молотилки, мм…………………………….…..1500
Диаметр барабана, мм….…………………………….….800
Частота вращения барабана, об/мин…….…….….512-954
Вместимость бункера зерна, м3……………………….….6
Мощность двигателя, л.с.…………………….…………235
Высота комбайна, м……………………………….………..4
Длина с копнителем и делителем, м…………………….11
Устройство
Комбайн «Дон-1500» (рис. 1) состоит из следующих составных частей: жатвенной части, платформы-подборщика, молотилки, оборудования для уборки незерновой части урожая, ходовой части, двигателя, гидравлической системы, системы электрооборудования, а также дополнительного оборудования.
Жатка фронтально навешена на молотилку, соединяется с проставкой посредством сферического шарнира 46 и механизма уравновешивания, во время работы опирается на почву двумя башмаками 1, копируя неровности поля в продольном и поперечном направлениях. Внутри проставки установлен промежуточный битер 7. Проставка жестко соединена с наклонной камерой 8, которая верхней частью шарнирно связана с корпусом молотилки, а нижней опирается на два гидравлических цилиндра 45, установленных на балке моста ведущих колес. В корпусе наклонной камеры находится плавающий транспортер 9. На жатке установлены мотовило 5, режущий аппарат 2, шнек 6 и механизмы привода рабочих органов.
Молотилка состоит из следующих основных частей и механизмов: молотильного аппарата, включающего бильный барабан 11, подбарабанье 43 и отбойный битер 14; соломотряса 33 и очистки, состоящей из транспортной доски 42, верхнего 31 и нижнего 32 решет, вентилятора 39, шнеков 30, 36 и домолачивающего устройства 35. На крыше молотилки установлен бункер для зерна 17.
Оборудование для сбора незерновой части урожая - копнитель 21, который крепится к задней части молотилки. Он включает в себя камеру и механизмы соломонабивателя 19 и половонабивателя 28. В зависимости от зоны применения комбайна он может быть оборудован измельчителем соломы или капотом для укладки соломы в валок.
Ходовая часть комбайна состоит из ведущего моста с колесами 44, механизма привода, коробки диапазонов скоростей, тормозной системы; моста управляемых колес 26 с гидравлическим управлением.
Гидравлическая система позволяет комбайнеру изменять режимы работы и параметры установки рабочих органов со своего рабочего места.
Силовая установка - дизельный двигатель СМД-31 А.
Кабина 12 - теплозвукоизолированная, имеет принудительную вентиляцию, может быть оборудована кондиционером. Для удобства работы механизатора сделаны две двери. В кабине сосредоточены все органы управления, приборы контроля и сигнализации.
Технологический процесс комбайна происходит следующим образом: при его движении по полю планки 4 вращающегося мотовила 5 погружаются в стеблевую массу, отделяют узкую полосу растений и подводят их к режущему аппарату 2.
Срезанные стебли мотовило перемещает дальше к шнеку жатки 6. Шнек спиралями левого и правого направлений подает стебли к центру жатки в зону пальчикового механизма, который захватывает срезанную массу и перемещает в окно жатки. Отсюда масса забирается битером 7 проставки и проталкивается в наклонную камеру 8 к плавающему транспортеру 9. Нижняя ветвь транспортера перемещает стебли в молотильный аппарат. Вращающийся молотильный барабан 11 наносит удары по хлебной массе и протаскивает ее по неподвижной деке, в результате чего зерно выделяется из колосьев. Большая часть зерна сепарируется через подбарабанье на транспортную доску 42 очистки. Оставшаяся масса (зерно и солома) с большой скоростью выбрасывается на вращающийся отбойный битер 14 отражается от его лопастей под острым углом, что приводит к снижению скорости потока, разрыхлению массы и выделению зерна. Остальной ворох направляется на переднюю часть соломотряса 33. Ступенчатые клавиши соломотряса, совершая круговое движение, интенсивно перетряхивают солому. Зерно и мелкие примеси просыпаются через отверстия клавиш и сходят по их наклонному дну на транспортную доску 42 очистки. Ступенчатые боковины клавиш перемещают солому к выходу из молотилки в зону действия соломонабивателя 19, который проталкивает солому в копнитель 21.
Зерновой ворох, выделенный молотильным барабаном и соломотрясом, попадает на совершающую колебательные движения транспортную доску 42 очистки, которая перемещает ворох на верхнее решето, соединенное с транспортной доской. Зерно просыпается между жалюзи верхнего решета 31 и попадает на нижнее решето 32 (колеблющееся навстречу верхнему). Пройдя нижнее решето, очищенное зерно попадает в зерновой шнек 36, которым оно подается в бункер 17. Решета продуваются потоком воздуха, который создается вентилятором 39. Воздушный поток выносит с решет в копнитель легкие примеси (полову).
С верхнего решета 31 примеси и необмолоченные колосья попадают на удлинитель верхнего решета 29, задача которого выделить из вороха, поступившего на него, необмолоченные колосья.
Зерноуборочный комбайн фирмы MASSEY FERGUSON «MF 36 RS»:
1 - жатка; 2 - механизм выравнивания; 3 - мотовило; 4 - шнек; 5 - транспортер; 6 - мост ведущих колес; 7 - вентилятор очистки; 8 - кабина; 9 - кондиционер; 10 - рабочие фары; 11 - молотильный барабан; 12 - роторный сепаратор; 13 - транспортная доска; 14 - решетный стан; 15 - соломотряс; 16 - шасси; 17 - мост управляемых колес; 18 - измельчитель соломы; 19 - бункер
уборка зерно культура
Удлинитель имеет поперечные и продольные жалюзи, что увеличивает выделение колосьев, а для снижения скорости перемещения вороха и увеличения времени для выделения колосьев удлинитель крепится к раме верхнего решета под небольшим углом. Необмолоченные колосья проваливаются через жалюзи удлинителя и попадают в колосовой шнек 30, который перемещает их в домолачивающее устройство 35.
Примеси, имеющие размер больше необмолоченного колоса (полова, сбоина), не проходят через жалюзи удлинителя, сходят с него и посредством половонабивателя 28 перемещаются в переднюю нижнюю часть копнителя 25.
Цель и содержание работы . Закрепить знания по устройству приемной камеры и молотильных аппаратов зерноуборочных комбайнов, полученные на теоретических занятиях. Научиться разбирать, собирать и регулировать на определенный режим работы однобарабанный молотильный аппарат. Изучить особенности конструкции и разборки двухбарабанного молотильного аппарата. Освоить установку промежуточного битера между барабанами при верхней и нижней подачах хлебной массы во второй барабан.
Оборудование рабочего места . Молотилка комбайна СК-5 и двухбарабанная молотилка комбайна CK-6-II или СКД-5 комплектные; ключи гаечные 5,5X7; 8Х10, 9Х11, 12Х14, 14Х17, 17Х19; сменные головки 12, 14, 17 и 19 (2 шт.); ключ для круглых гаек; молотки - 2 шт.; плоскогубцы 150 и 175, отвертка; бородок слесарный 2 и 4; щипцы для снятия и установки стопорных колец; крейц-мейсель слесарный 8X60°; штангенциркуль ЩЦ-1-0,1-125, выколотка для шпонок; молоток с медными бойками; тиски П-120; надставки для ослабления крепления подшипников на валу d=16 мм; l=300 мм и d=38 мм; l=120 мм; наставка специальная для вы-прессовки уплотнений; наставка для выпрессовки подшипников; надставка для выбивания оси d = 4 мм; l=150 мм; наставки для запрессовки манжет и подшипников; кувалда кузнечная, щуп, линейка l=300; подставка для молотильного барабана; ломик; напильник.
Порядок выполнения работы . Повторить материал об устройстве молотильных аппаратов комбайнов. Осмотреть приемные камеры и молотильные устройства комбайнов СК-5 и СКД-5 или CK-6-II. Найти приемный битер 1 (рис. 35), отражатель 2, переходной направляющий щиток 12, перекрывающий промежуток между дном наклонной камеры и входной частью молотильного устройства, передний фартук 11 с камнеуловителем и люками для удаления камней, барабан 3 с решеткой подбарабанья 7 и надставкой 10 и фартук 8, промежуточный битер 17 и сепарирующую решетку 18, установленные между барабанами 3 и 13 молотилки комбайна СКД-5, отсекатель 14 и второе подбарабанье 16.
Ознакомиться с устройством боковых панелей молотильных аппаратов, с креплением корпусов подшипников битеров и барабанов и обратить внимание на то, что в панелях молотильных аппаратов предусмотрены люки для установки и снятия битеров и молотильных барабанов.
Рассмотреть схему привода рабочих органов молотильных аппаратов, обратив внимание на то, что приемный битер как у одно-, так и у двухбарабанного комбайнов приводится в действие от верхнего вала транспортера наклонной камеры жатвенной части, а барабаны имеют индивидуальный привод от главного контрприводного вала через клиноременные вариаторы. Промежуточный битер приводится во вращение цепью от контрпривода выгрузного шнека через фрикционную предохранительную муфту. Привод отбойного битера комбайна СКД-5 осуществляется цепной передачей, на CK-6-II- клиноременной передачей от вала второго барабана, а на комбайне СК-5 - клиновыми ремнями от главного контрприводного вала с правой стороны молотилки.
Проверить наличие необходимого инструмента и приспособлений, подготовить рабочее место и приступить к выполнению работы.
Разборка молотильного аппарата комбайна СК-5
Выполнить подготовительные работы для доступа к молотильному аппарату :
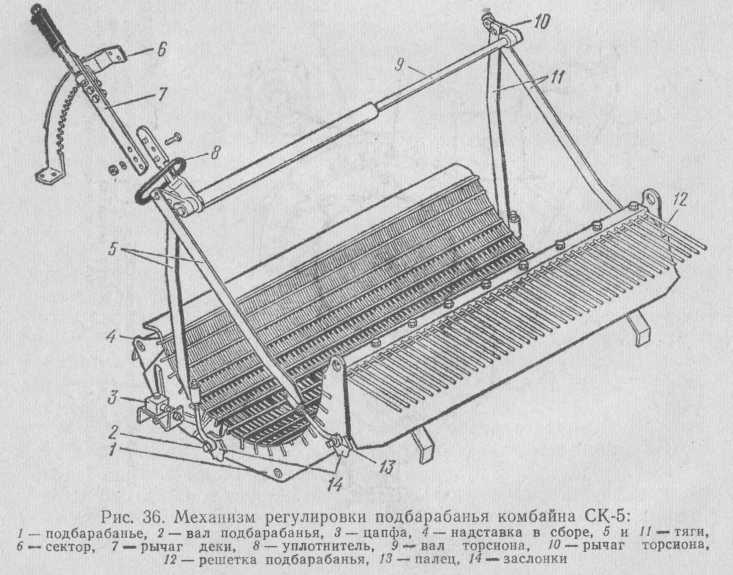
Снять и разобрать приемный битер :
- Отогнуть стопорную шайбу 9 (рис. 37), отвернуть гайку 8, снять звездочку 10 и выбить шпонку 6.
- Отвернуть гайки, снять крышку, вынуть болты из прорезей в корпусе подшипника и ослабить крепление подшипника 13 на цапфе 7.
- Отвернуть гайки 11 и снять с цапфы корпус 12 вместе с подшипником 13.
- Вывернуть болты крепления наружного фланца 3 к левой панели молотилки, вывести битер из приемной камеры и перенести на монтажный стол.
- Снять с внутренней стороны правой панели молотильного аппарата фланец 14 вместе с болтами.
- Отвернуть гайки, снять крышку, ослабить крепление подшипника 1 на левой цапфе и снять корпус 2 с подшипником 1, внешний фланец 3 и внутренний фланец 4.
Снять и разобрать механизм регулирования оборотов барабана :
- Ослабить натяжение цепей привода механизма регулирования оборотов барабана, найти соединительные звенья, разъединить их, снять цепь привода звездочки 2 (рис. 38), а затем цепь 7 и скобу 10 с натяжной звездочкой 9.
- Отвернуть гайки 4, вынуть винты 3 и снять поводки 5 и 6.
- Нажать на рукоятку 1 (рис. 39) динамометрической ручки 3 и, вращая ручку против часовой стрелки, развести диски большого шкива 11 на валу главного контрпривода и снять приводной ремень барабана.
- Вывернуть болты 2, снять динамометрическую ручку 3 в сборе и перенести ее на монтажный стол для разборки. Выбить шпонку из паза вала 30 и снять звездочку 4.
- Снять стопорное кольцо 5, вынуть два полукольца и шплинты, отвернуть корончатые гайки 6 на болтах, соединяющих шкив 11 с корпусом механизма регулирования, снять с вала главного контрпривода механизм регулирования 7 в сборе и выбить шпонку из паза вала 30.
- Отогнуть ушко стопорной шайбы 9, отвернуть гайку 8, снять шайбы 9 и 10, спрессовать большой шкив 11 с вала и выбить из паза вала длинную шпонку.
- Вынуть стопорное кольцо 22 (рис. 40), навернуть корпус механизма на втулку, снять два полукольца 21, механизм регулирования 17 в сборе, кольцо 3 и выбить шпонки из пазов вала 16.
- Наметить положение дисков 23 и 24 относительно друг друга, снять подвижный диск 23, спрессовать неподвижный диск 24, снять его с вала барабана 16 и выбить шпонку из паза.
- Разобрать динамометрическую ручку: отвернуть гайку 18 (см. рис. 38,6), снять шайбы, стрелку 19 и вынуть из стакана 13 болт 11; вывернуть болт 16, снять рукоятку 17 и вынуть пружину 21; расшплинтовать и вынуть ось 20, снять фиксатор 14 и пружину 15. Разобрать механизм регулирования 7 (см. рис. 39), снятый с вала 30 главного контрпривода, снять проволоку крепления колпака 11 (рис. 41) на корпусе 9, вывернуть втулку 13 из корпуса 9 и снять защитный колпак 11; вывернуть из корпуса 9 пробку и сапун 10 в сборе; вывернуть болты 1, снять крышку 2, прокладку 4, втулки о и 7 и корпус 9 в сборе; отвернуть гайки на винтах 12, снять поводок 6 (см. рис. 38), втулку 13 (см. рис. 41) в сборе, стопорное кольцо 23 и кольцо 22; выпрессовать каретку 15, снять конус 16, крышку 17, кольцо 18 и втулку 20; выпрессовать из втулок 5 и 20 наружные обоймы подшипников 6 и 21 и спрессовать внутренние обоймы с втулки 7 и каретки 15.
Механизм регулирования, снятый с вала молотильного барабана, имеет такое же устройство, как и механизм, установленный на валу главного контрпривода. Его разборка и сборка проводится в аналогичной последовательности.
Снять и разобрать молотильный барабан :
- Отвернуть гайки на болтах 7 (см. рис. 40), снять крышку 1 на левом конце вала барабана, отвернуть круглую гайку на конусной втулке и ослабить крепление подшипника 4 на валу 16.
- Отвернуть гайки на болтах крепления фланца 25 к левой панели молотилки, вынуть болты с внутренней стороны молотильного аппарата, снять с вала фланец в сборе с корпусом 6 и подшипником 4. Отвернуть гайки, вынуть болты и снять корпус с подшипником с фланца.
- Вывернуть болты и отвернуть гайки крепления фланца 12 к правой панели молотилки, вывести барабан в сборе с фланцем из молотильного аппарата и установить на специальную подставку.
- Отвернуть гайки, снять крышку 1 в сборе с манжетой 2, вынуть из пазов корпуса 6 болты 14. Ослабить крепление подшипника 4 на валу 16 барабана, снять фланец 12 в сборе с корпусом 6 и подшипником 4. Отвернуть гайки, вынуть болты и снять с фланца корпус с подшипником.
- Выбить специальные шпонки из пазов вала барабана 16 и вынуть вал барабана из ступиц остова 11.
- Отвернуть гайки на болтах со специальными головками и снять левые и правые бичи 10 и прокладки-подбичники с остова барабана (рис. 40).
Снять и разобрать отбойный битер :
- Отвернуть гайки 11 (рис. 42), снять шайбы 12 и кольцо 13, спрессовать с вала 5 двухручьевой шкив 14 и выбить из паза вала шпонку.
- Отвернуть гайки, снять крышку подшипника на правом конце вала битера, вынуть из пазов корпуса 15 болты, ослабить крепление подшипника 16 на валу, снять корпус подшипника 15 с фланцем 17 и успокоитель 18.
- Вывернуть болты крепления фланца 9 к левой панели молотильного аппарата и вывести из молотилки отбойный битер вместе с фланцем 9 и подшипником 8.
- Снять с вала корпус 7 с подшипником 8 и фланец 9, выполняя те же операции, что и на правом конце вала.
- Ослабить гайки 3, отвернуть винты 4 на ступицах 2. Легкими ударами молотка в торец сместить вал 5 в ступицах, вынуть его из корпуса 1 и выбить шпонки из пазов вала.
Снять подбарабанье молотильного устройства :
- Отвернуть гайки, вынуть болты и снять переднюю связь панелей молотилки.
- Вывернуть болты, снять передний фартук грохота, решетку 7 (см. рис. 35) и фартук 8 с последней планки подбарабанья 9.
- Вывернуть пальцы 13 (см. рис. 36) и выбить вал 2.
- Отвернуть гайки крепления цапф 3 к кронштейнам левой и правой панелей молотилки, ослабить регулировочные гайки и снять цапфы.
- Вынуть подбарабанье 1 и надставку 4 в сборе.
Закончив разборку молотильного аппарата, осмотреть состояние демонтированных узлов и деталей.
Ознакомиться с устройством приемной камеры молотильного аппарата, конструкцией приемного и отбойного битеров, способом крепления корпуса отбойного битера на валу.
Изучить устройство молотильного барабана, крепление остова барабана на валу. Выяснить различие бичей, снятых с барабана, способ их крепления. Заменить бичи, имеющие забоины и заусенцы. Обратить внимание на направление рифов двух соседних бичей; рифы должны быть направлены в разные стороны. Проверить торцовым ключом затяжку гаек на болтах крепления бичей к остову барабана. Поставить на место снятые прокладки-подбичники, бичи и надежно закрепить их болтами. Неплоскостность подбични-ков на всей длине допускается не более 2,0 мм.
Рассмотреть способ крепления неподвижного и подвижного дисков малого шкива на валу молотильного барабана.
Разобраться в устройстве механизма регулирования, выяснить назначение каждой детали, проверить их состояние и подготовить к сборке.
Уяснить разницу в конструкциях подшипников битеров и барабана в сравнении с подшипниками механизма регулирования. Проверить состояние уплотнителей, удерживающих смазку в подшипниках.
Осмотреть подбарабанье и надставку, обратить внимание на состояние поперечных планок и прутков. Для обеспечения нормального обмолота хлебной массы грани планок подбарабанья должны быть острыми, а прутки непогнутыми. Уяснить назначение цапф, пальцев, решетки подбарабанья и фартука.
Приступить к оборке и установке узлов молотильного аппарата в последовательности, обратной демонтажу.
Сборка молотильного аппарата комбайна СК-5
Установить подбарабанье молотильного устройства :
- Закрепить болтами к последней планке подбарабанья 9 (см. рис. 35) решетку 7 и соединить специальной осью фартук 8 с петлей.
- Проверить прочность крепления щитков к передней планке надставки 10 подбарабанья.
- Установить подбарабанье 1 (см. рис. 36) и надставку 4 в молотильное устройство, ввернуть пальцы 13, соединить подбарабанье с надставкой валом 2.
- Вставить в отверстия надставки 4 и опорных кронштейнов на панелях цапфы 3, закрепить их гайками снизу и затянуть боковые регулировочные гайки.
- Поставить на место фартук грохота и переднюю связь панелей молотильного аппарата, вставить болты, навернуть и затянуть гайки.
Собрать и установить отбойный битер :
- Вставить в пазы вала 5 (см. рис. 42) шпонки, ввести вал в ступицы 2 корпуса битера 1 так, чтобы от буртика вала до торца битера было 198,5± 1 мм, завернуть винты 4 и затянуть гайки 3.
- Поставить корпус 7 подшипника с фланцем 9 на вал 5. Затянуть конусную втулку подшипника 8 на валу, выдержав расстояние от торца битера до торца фланца 15,5 мм, установить крышку, вставить болты и затянуть гайки.
- Завести в верхний люк левой панели молотильного аппарата отбойный битер и закрепить фланец 9 болтами к панели молотильного аппарата.
- Надеть на правый конец вала битера успокоитель 18, фланец 17, корпус 15 с подшипником 16, закрепить болтами фланец и корпус подшипника, затянуть конусную втулку подшипника на валу, поставить крышку и закрепить ее болтами.
- Вставить в паз вала 5 шпонку, напрессовать на свободный конец двухручьевой шкив 14, установить кольцо 13, шайбы 12, навернуть гайки 11 и надежно их затянуть.
Собрать и установить молотильный барабан :
- Установить прокладки-подбичники, правые и левые бичи 10 (см. рис. 40) поочередно, вставить болты со специальными головками и затянуть гайки.
- Вставить вал 16 в ступицы остова барабана 11, забить до отказа специальные шпонки, выдержав расстояние от бурта вала до торца бича 38,5 мм. Проверить прочность крепления остова барабана на валу.
- Прикрепить к фланцу 12 корпус 6 в сборе с подшипником 4, установить фланец на правый конец вала барабана, вставить болты крепления фланца к панели молотилки, навернуть и затянуть гайки.
- Затянуть конусную втулку подшипника на валу 16, поставить и закрепить крышку 1 в сборе с манжетой 2.
- Соединить болтами фланец 25 с корпусом 6 в сборе с подшипником 4, надеть на левый конец вала барабана фланец, вставить с внутренней стороны панели молотильного аппарата болты крепления, навернуть и затянуть гайки.
- Закрепить конус подшипника на валу, напрессовать на вал кольцо, поставить крышку 1, вставить болты 18 и затянуть гайки. Проверить прочность крепления вала в подшипниках.
Собрать и установить приемный битер :
- Закрепить корпус 2 (см. рис. 37) в сборе с подшипником 1 на фланцы 3 и 4 болтами с полукруглыми головками. Установить корпус подшипника с фланцами на левую цапфу крыльчатки битера 5, затянуть конусную втулку подшипника так, чтобы от торца вала до торца корпуса подшипника было 8 мм. Поставить крышку, вставить болты и затянуть гайки.
- Ввести битер в люк левой панели молотильного аппарата и прикрепить внешний фланец 3 болтами к панели молотилки.
- Установить с внутренней стороны правой панели молотильного аппарата фланец 14 и вставить болты крепления.
- Надеть на правую цапфу крыльчатки битера 5 корпус 12 в сборе с подшипником 13, навернуть гайки на болты крепления фланца 14 к панели молотилки и затянуть их. Поставить крышку и закрепить ее болтами к корпусу подшипника 12.
- Вставить в паз вала шпонку 6, напрессовать на цапфу 7 звездочку 10, установить стопорную шайбу 9, затянуть гайку 8 и загнуть ушко шайбы.
Установить узлы и детали, снятые для доступа к молотильному аппарату :
- Надеть на вал 2 (см. рис. 36) и пальцы 13 заслонки 14 овальных отверстий в панелях молотилки. Установить тяги 5 и 11 в сборе с винтовыми подвесками и зашплинтовать их.
- Проверить перемещение подбарабанья рычагом 7 из верхнего в нижнее положение, и наоборот.
- Установить на левой панели молотильного аппарата вертикальную тягу стояночного тормоза и горизонтальную проволочную тягу механизма выгрузки соломы из копнителя, вставить в отверстие вилок соединительные пальцы и зашплинтовать их.
- Надеть ремень привода отбойного битера, проворачивая ломиком вал барабана с правой стороны.
- Закрепить болтами с полукруглыми головками желоб-успокоитель нижней ветви ремня привода жатки.
- Установить кронштейн и вал контрпривода в сборе с корпусом подшипника и приводной звездочкой, поставить на место натяжной шкив в сборе клинового ремня верхнего вала транспортера наклонной камеры и закрепить их.
- Закрепить на правом конце вала барабана корпус привода тахометра, освободить прикрепленный на тяге механизма выключения выгрузного шнека трос тахометра, вставить конец троса в корпус привода, навернуть и затянуть соединительную гайку.
- Привернуть верхнюю подвеску и задний кронштейн для крепления правого щита молотилки и поставить щиты ограждения механизмов передач на передней части молотилки и щиток ограждения цепной передачи на выгрузной шнек.
Выполнить регулировки молотильного аппарата :
- Натянуть ремень привода барабана комбайна СК-5 так, чтобы под действием усилия 4 кгс (39,2 Н) его прогиб в средней части между осями шкивов был 2-3 мм. Чрезмерное натяжение приводного ремня приводит к его быстрому износу, а также к изгибу валов барабана и контрпривода. Натягивают ремень при минимальных устойчивых оборотах двигателя комбайна. Для этого необходимо включить привод рабочих органов молотилки, прижать ручку фиксатора 3 (рис. 43) к рукоятке 4, вывести выступы фиксатора из зацепления со звездочкой 2 и вращать рукоятку 4 по часовой стрелке, натянуть ремень до тех пор, пока стрелка переместится на метку 6 рукоятки 4. Это будет соответствовать нормальному натяжению ремня.
Аналогично натягивают ремень вариатора второго барабана комбайна CK-6-II. Ремни привода барабанов комбайна СКД-5 натягивают равномерным сближением дисков шкивов барабана и главного контрпривода. - Отрегулировать обороты барабана так, чтобы стрелка тахометра совпала с делением 1050. На комбайнах СК-5 и СК-6 эта регулировка выполняется из кабины комбайнера вращением рукоятки цепного привода механизма регулирования оборотов барабана. Для увеличения оборотов рукоятку следует вращать по часовой стрелке, для уменьшения - против часовой стрелки.
Применительно к убираемым культурам и состоянию хлебной массы обороты молотильных барабанов этих комбайнов можно изменять в пределах 750-1365 об/мин, а после перестановки шкивов - от 415 до 750 об/мин.
Число оборотов молотильных барабанов комбайна CK-6-II можно изменять в диапазоне 743-1365 об/мин, а после перестановки шкивов - от 415 до 750 об/мин.
Для изменения числа оборотов барабана необходимо включить рабочие органы молотилки комбайна, перевести двигатель на полные обороты, вытянуть до отказа на себя упор 8 {см. рис. 43) на звездочке 2 и повернуть его против часовой стрелки на 90°. Затем, вращая рукоятку 4 механизма регулирования 1 и возвращая упор 8 в исходное положение через каждые полоборота рукоятки, установить по тахометру необходимое число оборотов. При этом необходимо иметь в виду, что один полный оборот рукоятки изменяет частоту вращения барабана на 100 об/мин.
Во время регулировки оборотов барабана нельзя нажимать на ручку фиксатора 3 и выводить его из зацепления с венцом 7, так как это приведет к изменению натяжения или ослабления ремня.
Аналогично следует отрегулировать обороты второго молотильного барабана динамометрической ручкой, установленной на другом конце вала главного контрпривода.
Обороты барабанов комбайна СКД-5 изменяются в пределах 430-1390 в минуту перемещением дисков шкивов и перестановкой шкивов при неработающем двигателе. Диски шкивов равномерна раздвигают и сближают стяжными и распорными болтами, проверяют шаблоном положение регулируемого диска относительно неподвижного, вовремя устраняя перекос, и равномерно с усилием 5 кгс (49,03 Н) затягивают гайки на стяжных и распорных болтах.
Увеличение расстояния между дисками шкива блока вариатора главного контрпривода на 3 мм и уменьшение расстояния между дисками шкива молотильного барабана на такую же величину изменяет число оборотов барабана примерно на 50 в минуту.
Во время уборки труднообмолачиваемых культур и сортов, а также хлебов с большой влажностью следует увеличивать числа оборотов барабанов и уменьшать зазоры между бичами барабана и подбарабаньем. Хлеба с нормальной влажностью убирают при оптимальных оборотах барабанов и увеличивают зазоры до пределов, при которых потери от недомолота не превышали бы предела, установленного агротехническими требованиями уборки.
Для обмолота пшеницы оптимальные обороты барабана 900- 1150 в минуту, ржи и ячменя - от 850 до 1000 и подсолнечника - 350-550 об/мин.
Как правило, при недостаточных оборотах барабана появляется недомолот, а при повышенных - дробление зерна.
- Установить зазоры в одно- и двухбарабанном молотильных устройствах по заданию преподавателя.
Зазоры между планками подбарабанья и бичами барабана молотильного устройства при уборке определенной культуры регулируют из кабины комбайнера рычагом 7 (см. рис. 36).
Установочную регулировку подбарабанья комбайнов СК-5, СК-6 и первого барабана комбайнов СК-6-П и СКД-6 следует выполнить в такой последовательности. Переместить рычаг 7 в крайнее заднее положение и зафиксировать его на первом вырезе сектора 6, открыть смотровые люки на панелях молотилки. Изменением длины тяг 5 я 11 нижними, или верхними, регулировочными гайками и гайками цапф 3 в однобарабанных молотильных устройствах комбайнов СК-5 и СК-6 установить зазор на входе 18 мм, между передней планкой основного подбарабанья 1 и бичами барабана 14 мм и на выходе 2 мм.
В молотильных устройствах первого барабана комбайнов СКД-5 и CK-6-II установить зазоры соответственно: на входе 14 мм, на выходе 2 мм.
Для установочной регулировки второго подбарабанья комбайнов СКД-5 и СК-6-П рычаг подбарабанья 16 (см. рис. 35) и 10 (рис. 44) установить на первый передний вырез сектора и тягами подбарабанья отрегулировать зазоры между бичами барабана и планками подбарабанья комбайна СКД-5: на входе 14 мм, на выходе 2 мм, а комбайна CK-6-II: на входе 18 мм, в основном подба-рабанье 14 мм и на выходе 2 мм.
Проверить зазоры щупом через люки левой и правой панелей молотильного аппарата, отвернуть винт и переместить шкалу, совмещая цифры 18, 14 и 2 со стрелкой рычага, и надежно затянуть все гайки.
Прокрутить вручную каждый барабан и убедиться в отсутствии задевания бичей за планки подбарабанья.
Во время работы комбайнов применительно к состоянию убираемой культуры и влажности хлебной массы зазоры можно изменять в следующих пределах: на входе надставки подбарабанья от 18 до 48 мм, на основном подбарабанье от 14 до 46 мм и на выходе от 2 до 42 мм.
При уборке зерновых культур в период полной спелости зерна и нормальной влажности хлебной массы зазоры на входе устанавливают 20 мм, между передней планкой основного подбарабанья и бичами барабана 16 мм и на выходе 4 мм.
Особенности конструкции и разборки двухбарабанного молотильного аппарата комбайнов СК-5 и CK-6-II
- Главное отличие молотильного аппарата комбайна СКД-5 от молотильного устройства комбайнов СК-5 и СК-6 заключается в том, что он состоит из двух барабанов 3 я 13 (см. рис. 35) биль-ного типа и обеспечивает двухступенчатый обмолот зерновых и зернобобовых культур. Аналогичный молотильный аппарат, но с другими параметрами имеет двухбарабанная модификация комбайна СК-6-П.
- Между барабанами молотильных аппаратов комбайнов СКД-5 и СК-6-П установлены сепарирующая решетка 18 и промежуточный битер 17.
- Подбарабанья 9 и 16 комбайна СКД-5 односекционные, решетчатые, с углом обхвата каждого барабана 127°. Расстояние между прутками увеличено до 16,5 мм. Подбарабанье первого барабана комбайна CK-6-II односекционное с углом обхвата 96°, второго- двухсекционное, решетчатое, обратимое, с углом обхвата барабана 146°.
- Молотильные барабаны комбайна СКД-5 имеют диаметр 550 мм, длину 1186 мм, диаметры валов 55 мм. Параметры барабанов комбайна CK-6-II такие же, как и у СК-6: длина барабанов 1485 мм, диаметр 600 мм.
- Панели двухбарабанных молотильных аппаратов состоят из двух секций. Съемные вторые секции дают возможность легко демонтировать и устанавливать второй барабан и отбойный битер.
- Сепарирующая решетка присоединена к первому подбара-банью шарнирно и свободно опирается на планку второго подбарабанья.
- Отсекатели 4 к 14 (см. рис. 35), расположенные между барабанами и битерами, препятствуют выносу соломы.
- Дополнительный рычаг, выведенный в отверстие верхнего листа крыши молотилки, позволяет осуществлять регулировку зазоров вторым барабаном и подбарабаньем.
- Второй молотильный барабан комбайна СКД-5, как и первый, получает привод от двухручьевого блока вариатора, установленного на левом конце главного контрприводного вала. Молотильные барабаны комбайна CK-6-II получают привод от вариаторов; установленных на разных концах главного контрприводного вала, и имеют автономные механизмы регулирования оборотов. Второй барабан отличается длиной вала и наличием на валу шкива привода отбойного битера.
- Для демонтажа второго барабана, отбойного битера и под-барабанья молотильного аппарата комбайна СКД-5 необходимо снять щиток ограждения двигателя на правой стороне молотилки:
- ослабить натяжение, снять приводную цепь и звездочку с вала отбойного битера;
- снять крышки и ослабить крепление подшипников на валу отбойного битера;
- отвернуть болты крепления, снять правую верхнюю секцию панели молотильного аппарата и вынуть через образовавшийся люк отбойный битер;
- развести диски вариаторов, снять ремень привода второго барабана и ремни главного контрпривода вала;
- спрессовать с вала барабана шкив, отвернуть болты и снять верхнюю левую секцию панели молотильного аппарата;
- отвернуть гайки, вынуть болты крепления корпусов подшипников барабана и снять нижнюю левую секцию панели;
- вывести барабан из молотилки и установить на специальную подставку;
- снять направляющую решетку отбойного битера, клавиши соломотряса, выбить валы и вынуть из молотилки подбарабанье.
После осмотра и ознакомления с устройством снятых узлов установить на место молотильный барабан, отбойный битер и подбарабанье в последовательности, обратной разборке.
Переставить промежуточный битер комбайна CK-6-II из верхнего положения в нижнее :
- Ослабить натяжение цепи привода битера 4 (см. рис. 44), найти и разъединить соединительное звено, снять цепь и приводную звездочку битера.
- Отвернуть гайки, снять крышки, вынуть болты и ослабить крепление подшипников 12 и 15 (рис. 45) на концах вала 4 корпуса битера 8.
- Вывернуть болты 2, снять фланец 1 вместе с правым подшипником 15, корпусом 14 и диском 3, вывести битер через люк и положить на монтажный стол.
- Установить подбарабанья так, чтобы ось шомпола 15 (см. рис. 44) совпадала с отверстием в панели молотильного устройства, и выбить шомпол из ушек.
- Вывернуть направляющие болты и вынуть через люк доску 12, решетку подбарабанья 14 и щиток 13.
- Установить между барабанами сепарирующую решетку 17 и соединить ее шомполом 15 с петлей подбарабанья 16.
- Ослабить контргайки 6 (см. рис. 45), отвернуть винты 7 на ступицах 5, снять с вала корпус битера 8, развернуть его на 180°, установить симметрично шпонкам и закрепить стопорными винтами 7 на валу 4.
- Отвернуть гайки, вынуть болты с полукруглыми головками, снять диск 7 (рис. 46) и фланец 1 и поменять их местами, а освободившиеся отверстия заглушить болтами.
- Ввести битер в молотильный аппарат, установить на левый конец вала фланец в сборе с подшипником 15, повернуть фланец 1 (см. рис. 45) и прикрепить его к панели болтами 2. Затянуть конусные втулки подшипников 12 и 15, закрыть подшипники крышками, надеть на вал приводную звездочку 10 и закрепить ее на валу 4 шпонкой 9.
- Переставить кронштейн 3 (см. рис. 46) с натяжной звездочкой в нижнее положение, изменить схему привода битера, укоротить цепь до 46 звеньев, надеть ее и натянуть перемещением звездочки при помощи кронштейна 3.
Переставить промежуточный битер комбайна CK-6-II из ни нижнего положения в верхнее :
- Выполнить демонтажные операции 1, 2, 3, 4 и 7 в такой же последовательности, как и при перестановке промежуточного битера из верхнего положения в нижнее.
- Вынуть из молотильного аппарата сепарирующую решетку 17 (см. рис. 44).
- Поменять местами диск 7 (см. рис. 46) и фланец на правой панели 9 молотильного аппарата.
- Переставить кронштейн с натяжной звездочкой 3 в верхнее положение. При этом три болта 2 вставить с внутренней стороны панели молотилки, а болт 6 ввернуть в гайку диска 7. Свободные отверстия заглушить болтами.
- Установить щиток 13 (см. рис. 44), направляющую доску 12 и решетку подбарабанья 14 и закрепить их болтами.
- Ввести битер 4 в молотильный аппарат, установить его в верхнее положение над щитком 13, поставить на правый конец вала корпус с подшипником 12 (см. рис. 45) и прикрепить его к панели.
- Установить фланец 1 с корпусом 14 и подшипником 15 на левом конце вала 4, прикрепить его болтами к панели молотильного аппарата, затянуть конусные втулки подшипников 12 и 15, поставить на место и закрепить болтами крышки.
- Надеть на правый конец вала звездочку 10, установить ее в одну плоскость с другими звездочками контура и закрепить звездочку на валу 4 шпонкой 9.
- Удлинить цепь до 74 звеньев, надеть ее, как показано на рис. 45, и натянуть кронштейном 3 с натяжной звездочкой.
Положение промежуточного битера между барабанами изменяют в зависимости от состояния убираемой культуры и погодных условий уборки.
В верхнем положении промежуточный битер вращается в направлении, противоположном молотильным барабанам, и более энергично воздействует на хлебную массу. Это дает возможность более качественно обмолачивать длинностебельные и переувлажненные зерновые культуры и выделять из хлебной массы свободное зерно., обмолоченное первым барабаном.
Для уборки зерновых культур со средним стеблестоем и нормальной по влажности хлебной массы обмолот целесообразнее проводить при нижнем положении промежуточного битера.
В нижнем положении промежуточный битер способствует повышению пропускной способности молотильного аппарата и обеспечивает хорошую сепарацию зерна, обмолоченного первым барабаном, через решетку, установленную между барабанами.
Способы уборки зерновых
Зерновые колосовые культуры в настоящее время убирают двумя способами: однофазным (прямым комбайнированием) и двухфазным (раздельным).Однофазный способ, или прямая комбайновая уборка, проводится на полностью созревших, чистых от сорняков и не полеглых хлебных массивах. В этом случае комбайн за один проход по полю полностью завершает все уборочные операции: скашивание, обмолот и очистку зерна, сбор не зерновой части урожая (соломы и половы) в виде копен, уложенных на поле.
Двухфазный раздельный способ состоит в скашивании хлебной массы с укладкой в валки специальными катками, навешиваемыми на комбайны или прицепляемыми к тракторам. В этом случаем скашивание и укладку в валки хлебной массы проводят при восковой спелости зерна, которое дозревает и высыхает в валках в течение 4...8 дней После этого валки подбирают комбайнами, оборудованными подборщиками. В остальном работа комбайна остается такой же, как при однофазном способе.
Раздельным способом убирают поля, засеянные неравномерно созревающими культурами: (просо, овес), склонными к полеганию или обсыпанию, а также при наличии сорняков.
Хлеба, скошенные и уложенные в валки, быстрее, чем на корню, и равномернее дозревают и высыхают. Работа комбайна при подборе валков значительно облегчается, зерно получается более чистым и сухим.
Раздельная уборка обеспечивает при благоприятных погодных условиях повышение сбора зерна до 4 ц/га за счет снижения потерь.
Агротехнические требования
-
Густота стеблестоя на участках
для раздельного способа уборки
должна быть не менее 250...300 растений на
1 кв.м, а высота не менее 60...80 см.
Высота среза растения должна быть в пределах 12...25 см
Жатки должны обеспечивать формирование валков, массой не менее 1,5 кг на 1 м его длины, а шириной 1,4...1,6 м.
Потери зерна после прохода жатки не должны превышать0,5%при скашивании прямостоящих хлебов и 1,5% при скашивании полеглых
Потери зерна за подборщиком не должны превышать 0,5 %
Общие потери за молотилкой (недомолотом и невытрясом) должны быть не более 1,5% при уборке хлебов с влажностью зерна до 18%
Дробление и обрушивание продовольственного зерна не должно превышать 2% при уборке колосовых культур и 3%-крупяных
Содержание сорных примесей в бункере не должно превышать 3%
Общее устройство комбайна
Комбайн состоит из жатки (хедера), подборщика, молотилки, устройства для сбора незерновой части урожая (копнителя или измельчителя), ходовой части и двигателя.Комбайн оборудован также электрической и гидравлической системами. Каждая из частей комбайна в свою очередь состоит из соответствующих узлов и механизмов.
Комбайновая жатка (хедер) включает в себя корпус с копирующими башмаками и шнеком, наклонную камеру с плавающим транспортером, механизмы подвески и уравновешивания, мотовило с механизмом регулирования положения и вариатором частоты вращения, режущий аппарат с механизмом привода и делители.
Все комбайновые жатки имеют в основном одинаковое устройство. Они отличаются лишь шириной захвата (4,1; 5,0; 6,0; 7,0; 8,6).
Молотилка состоит из молотильного устройства, соломотряса, очистки с транспортирующими устройствами (шнеками и элеваторами), системы механизмов привода, регулирования и сигнализации.
Копнитель представляет собой камеру, оборудованную соломонабивателем, половонабивателем, механизмом выгрузки и гидросистемой закрытия заднего клапана.
В определенных условиях вместо копнителя на комбайн навешивают измельчитель, который состоит из измельчающего барабана, противорежущего устройства, консольного шнека и вентилятора.
Ходовая часть включает в себя вариатор и мосты ведущих и управляемых колес. Мост ведущих колес, в свою очередь, состоит из муфты сцепления, коробки передач, дифференциала, двух бортовых редукторов, ведущих колес и тормозной системы.
Двигатели комбайнов являются модификациями тракторных двигателей.
Гидравлические системы комбайна предназначены для облегчения труда водителя по управлению машиной ивыполнению трудоемких регулировок.
При помощи гидравлических устройств выполняют подъем и опускание жатки, перемещение мотовила в вертикальном и горизонтальном направлениях, регулирование частоты вращения мотовила и механизма подборщика, регулирование скорости движения комбайна, управление копнителем и рулевой трапецией, перевод выгрузного шнека в рабочее и транспортное положения, управление частотой вращения барабанов молотильного устройства, отключение привода на механизмы жатки.
Устройство молотилки
Молотильный аппарат
В передней части корпуса молотилки имеется приемная камера, в которую плавающий транспортер жатки подает хлебную массу. В камере установлен приемный битер 1 (рис. 1), который представляет собой трубу с четырьмя отклоненными назад лопастями с зубчатыми кромками. Этими лопастями битер захватывает хлебную массу и направляет в молотильный аппарат.Молотильный аппарат состоит из двух барабанов 2 и 4 бильного типа. Между ними установлен промежуточный битер 3 с сепарирующей решеткой 13.За вторым барабаном расположен отбойный битер с направляющей решеткой 10.С нижней стороны оба барабана охватываются решетчатыми подбарабаньями 11 и 14.
Каждый барабан состоит из вала, двух крайних ведущих дисков со ступицами, закрепленными на валу шпонками, двух промежуточных кольцевых дисков и одного центрального диска, ступица которого установлена на валу с зазором равным 1 мм. Такая установка центрального диска позволяет ограничить прогиб вала от действия усилия натяжения приводных ремней.
На цилиндрической поверхности, образованной ведущими и промежуточными дисками и кольцами, закреплены восемь подбичников, к которым с помощью болтов крепятся бичи, имеющие правое и левое направление рифов. Бичи с правым и левым направлениями рифов устанавливаются на подбичниках через один.
При уборке длинносоломистых или влажных хлебов, при подборе неравномерно уложенных валков возможны случаи забивания молотильного аппарата хлебной массой. Наиболее эффективным способом его очистки является возможность сообщать барабану вращение в обратную сторону. Для этой цели на комбайне «Енисей» имеется устройство (рис. 2) позволяющее прокручивать первый молотильный барабан в обратную сторону с помощью гидроцилиндра.
На правом конце вала барабана установлены храповик 3 и диск 1с рычагом. Рычаг присоединен к штоку гидроцилиндра 4. В устройстве механизма имеются два подпружных фиксатора 2 и 5. При нормальной работе комбайна оба фиксатора выведены из зацепления с храповиком 3. Поэтому храповик, соединенный с валом барабана при помощи шпонки, вращается заодно с ними, а диск 1 с рычагом, установленный на валу при помощи подшипников не вращается.
Полости гидроцилиндра устройства обратной прокрутки барабана соединены с полостями гидроцилиндра механизма отключения привода жатки. При включении и выключении привода жатки шток гидроцилиндра обратной прокрутки также перемещается. Но поскольку фиксаторы выведены из зацепления с храповиком, то диск проворачивается гидроцилиндром в холостую.
Чтобы прокрутить барабан в обратную сторону (механизм его привода отключен), в зацепление с храповиком вводят оба фиксатора, провернув их на 90 0 . Перемещают рукоятку управления золотником секции отключения жатки в прямом и обратном направлениях, в результате чего гидроцилиндр прокручивает барабан в обратную сторону при данном положении золотника и при обратном шток гидроцилиндра обратной прокрутки возвращается в исходное положение. После очистки барабана фиксаторы выводят из зацепления с храповиком, оттянув их за ручки,повернув на 90 0 и установив в имеющиеся пазы.
Подбарабанья 11, 14 (см. Рис.1) обоих барабанов односекционные, с углом охвата 127 0 сварной конструкции. Каждое из них состоит из двух боковин, установленных на расстоянии друг от друга, равной рабочей длине барабана. Боковины соединены между собой планками прямоугольного сечения, параллельными оси барабана и установленными с переменным шагом. Между средними планками расстояния наибольшие, а между остальными в обоих направлениях расстояния убывают в одинаковой степени. Симметричность конструкции подбарабанья обеспечивает его обратимость, т.е. В случае износа передних кромок поперечных планок, подбарабанье можно снять, повернуть на 180 0 в горизонтальной плоскости и вновь установить. В этом случае изношенные кромки будут обращены назад по направлению вращения барабана.
Решетчатая поверхность подбарабанья образована прутками, пропущенными через поперечные планки на одинаковом расстоянии друг от друга в направлении оси барабана.
Подбарабанья (деки) (рис. 3) 13 и 9 на корпусе молотилки установлены с помощью валов торсинов 10 и 7 и подвесок 14. Подбарабанья с подвесками соединены регулировочными болтами 12. Изменение положения дек относительно барабанов осуществляется из кабины с помощью рычагов 2, 3, которые фиксируются в соответствующих пазах на зубчатых секторах. Таким образом обеспечивается регулирование зазоров между барабанами и подбарабаньями. Пружины 8 облегчают перемещение дек с помощью рычагов 2 и 3.
Соломотряс
Соломотряс 6 (рис.1) предназначен для выделения зерна из соломы и транспортирования соломы в копнитель. Рабочими органами соломотряса являются четыре клавиши.Каждая клавиша представляет собой узкий желоб из оцинкованной листовой стали, закрытой сверху жалюзийным решетом с постоянным углом наклона жалюзи (45 0). Верхние части боковин клавиши изготовлены в виде гребенчатых уступов (каскадов). Под первым каскадом клавиш отсутствует днище, а сверху над вторым каскадом установлен фартук из плотной ткани, который способствует снижению потерь зерна за соломотрясом за счет некоторого торможения соломистой массы и улавливания зерна выброшенным барабаном.
Над задними концами клавиш под крышей молотилки установлен клапанный сигнализатор забивания соломотряса соломой.
Клавиши соломотряса установлены на двух коленчатых валах, которые закреплены на боковинах молотилки, с помощью шарикоподшипников одноразовой смазки. В корпусах подшипников ведомого вала установлены резиновые амортизаторы, которые компенсируют возможные перекосы клавиш из-за неточностей сборки или изготовления деталей. Частота вращения валов равна 195 об/мин. Клавиши к коленчатым валам присоединены с помощью деревянных подшипников.
Механизм привода клавиш соломотряса обеспечивает подбрасывание и скольжение соломистой массы в направлении к копнителю. Такое воздействие способствует интенсивному выделению зерна из соломы.
Очистка
Очистка предназначена для выделения зерна из зернового вороха (его состав по массе: 60...75% зерна, до 25% половы, сбоины и 1...2% необмолоченных колосьев). Система очистки комбайна состоит из транспортной доски 1 (рис. 4), пальцевой решётки 11, двух станов 6 и 9 с решётами верхним 8 и нижним 7, удлинителя верхнего решета 12, вентилятора 4 и механизма привода. Транспортную доску с пальцевой решёткой, верхний стан с решетом и удлинителем в сборе называют грохотом.Транспортная доска 1 имеет ступенчатую поверхность и продольные гребёнки 20, предотвращающие смещение зернового вороха в одну сторону при поперечном наклоне комбайна и улучшающие транспортирование соломистой части вороха. На заднем поперечном брусе транспортной доски закреплена пальцевая решётка 11.
Верхний решётный стан 9 с жалюзийным решетом 8 присоединён к транспортной доске и является её продолжением. К задней планке верхнего решета присоединён удлинитель 12, снабжённый регулируемыми жалюзи. Раствор жалюзи регулируется с помощью рычага 15. Угол наклона удлинителя к плоскости решета можно регулировать и в нужном положении фиксировать с помощью болта 14, переставляя его в отверстиях боковины.
Передняя часть транспортной доски 1 подвешена к раме молотилки на деревянных подвесках 2, а задняя - с помощью трубчатой оси 18 через резиновые втулки соединена с верхними головками двуплечих рычагов 17 и шатунами 3колебательного вала 19. В задней части грохот соединён с рамой молотилки с помощью металлических подвесок 13.
Нижний решётный стан 6 представляет собой металлический короб со скатным дном и размещённым в верхней его части жалюзийным решетом 7, размер жалюзи которого меньше, чем у верхнего решета 8. Кроме того имеется возможность установить это решето с разными углами наклонена в продольном направлении, для чего предусмотрены регулировочные отверстия. Степень открытия жалюзи обоих решёт производится рычажным механизмом, расположенным с левой стороны комбайна.
Задняя часть левого стана 6 подвешена к раме молотилки с помощью металлических подвесок 13, а передняя часть соединена трубчатой осью 16 с нижними головками двуплечих рычагов 17.
Механизм привода решётных станов состоит из коленчатого (колебательного) вала 19, двух шатунов 3 и двух двуплечих рычагов 17. Коленчатый вал приводится в движение с левой стороны комбайна цепной передачей от вала вентилятора.
Вращение коленчатого вала через шатуны и двуплечие рычаги преобразуется в колебательные встречные движения грохота и нижнего решетного стана.
Для повышения эффективности работы очистки на комбайнах применяют вентиляторы 4. Основным рабочим органом вентилятора является пятилопастной крылач, вращающийся в цилиндрическом кожухе. Кожух вентилятора имеет окна для всасывания воздуха и наклонно расположенный канал прямоугольного сечения для направления воздушного потока под решета очистки.
У комбайна «Енисей» частота вращения крылача вентилятора постоянная. Интенсивность (мощность) воздушного потока регулируется изменением входной площади боковых окон кожуха вентилятора при помощи заслонок.
Привод и фиксирование заслонок в нужном положении осуществляется при помощи рычажного механизма, расположенного на левой стороне молотилки.
Гидрофицированный копнитель
Назначение и общее устройство
Копнитель предназначен для сбора соломы и половы, формирование копны путем подпрессовки собранной массы и выгрузки копны на поверхность поля. Копнитель закреплен в задней части корпуса молотилки и состоит из камеры, образованной двумя боковинами 11 (рис.5), каждая из которых имеет окно для выхода воздуха при заполнении копнителя, который поступает от вентилятора очистки, решетчатой крышкой 7,задним клапаном 9, днищем 13 с пальцами 12.В состав копнителя входят также соломонабиватель, половонабиватель, механизма выгрузки, включающего в себя предохранительную муфту и автомат выгрузки, гидравлическая система закрытия заднего клапана 9.
Днище 13 копнителя состоит из передней платформенной части и шарнирно присоединенных к ней пальцев 12. Пальцы 12 к платформенной части присоединены через промежуточные звенья, способствующие лучшему копированию пальцами рельефа поля и исключающие поломки пальцев при выгрузке копны. Под платформенной частью днища установлены две пружины 14, которые способствуют быстрому опусканию днища в процессе выгрузки.
Клапан 9, образующий заднюю стенку камеры копнителя, шарнирно подвешен на боковинах 11 в верхней их части. В задней части боковины установлены защелки 8, с помощью которых клапан удерживается от поворота при заполнении копнителя соломой.
Днище 13 копнителя и клапан соединены между собой тягами 27, обеспечивающими их взаимодействие.
Это происходит при выгрузке копны и закрытии клапана после нее. Возврат клапана в исходное положение после выгрузки копны осуществляется с помощью гидрофицированного механизма, состоящего из датчика 10,шарнирно соединенного с левой боковиной и постоянно удерживаемого в крайнем переднем положении пружиной 23. В исходном положении датчика 10 его упор 22 прижат к поворотному рычагу 26, который имеет общую с датчиком ось вращения. Поворотный рычаг 26 с помощью тяги 21 соединен с одним плечом двуплечного рычага 25. Упор 20 на клапане ограничивает поворот двуплечного рычага 25 против часовой стрелки и устанавливает поворотный рычаг 26 через тягу 21 в такое положение, при котором датчик 10 откланяется несколько назад, но не доходит до планок клапана 9,который занимает вертикальное положение в период заполнения копнителя. Второе плечо двуплечего рычага 25 соединено тягой 18 с рычагом управления положением золотника гидрораспределителя 16. Который служит для направления потока масла от насоса гидросистемы комбайна к другим потребителям при закрытом копнителе и подаче масла на слив из гидроцилиндров 19 при выгрузке копны. Гидроцилиндры 19 служат для возврата клапана 9 и днища 13 в положение для сбора соломы в копнителе. При возврате клапана гидрораспределитель переключается на подачу масла в гидроцилиндр 19.
Выгрузка копны происходит с помощью шарнирного тягово-рычажного механизма, связывающего защёлки 8 с педалью 24, расположенной в кабине комбайнёра. При нажатии на педаль при заполненном копнителе освобождают клапан 9 от удерживающей его связи с боковинами под действием веса копны и пружин 14 днище опускается и платформенная её часть занимает вертикальное положение, а пальцы 12 скользят по поверхности поля. Одновременно с опусканием днища клапан 9 под действием тяг 27, открывается и копна выходит из копнителя под действием сил трения между её основанием и поверхностью поля. В момент открытия клапана масло из гидроцилиндров 19 через распределитель 16 стекает в резервуар гидросистемы комбайна.
При открытом клапане его упор 20 отходит от двуплечего рычага 25 и не ограничивает его поворот против часовой стрелки.
Датчик 10 при выгрузке копны под действием пружины прижат к её поверхности и скользит по ней. После выхода копны из копнителя он продолжает своё движение в крайнее переднее положение. Упор 22 датчика воздействует на поворотный рычаг 26, который через тягу 21 перемещает двуплечий рычаг 25 против часовой стрелки. При повороте этого рычага его нижнее плечо через тягу 18 приводит золотник гидрораспределителя 16 в крайнее правое положение. В этом положении золотника масло от насоса гидросистемы комбайна направляется в гидроцилиндры 19, которые закрывают клапан 9 и через тяги 27 поднимают днище, копнителя в исходное положение. В момент, когда клапан занимает вертикальное положение, его упор 20 перемещает двуплечий рычаг по часовой стрелке. В результате чего натяжение тяги 18 исчезает, и золотник под действием собственной пружины возвращается в крайнее левое положение.
Соломонабиватель и половонабиватель
Соломонабиватель предназначен для транспортирования соломы от клавиш 1 соломотряса в камеру копнителя через подпрессовочную зону, образованную консольными брусьями 4 и лотком 2 .Соломонабиватель состоит из двух коленчатых валов 5, колена которых смещены относительно друг друга на 180 0 . На обоих валах на деревянных подшипниках установлены граблины 6 с зубьями 3. Граблины с боковинами 11 копнителя соединены шарнирно с помощью кулис 28. Коленчатые валы снабжены противовесами для уравновешивания вращающихся частей соломонабивателя.
Зубья 3 граблины в процессе работы перемещаются между консольными брусьями 4, которые установлены с наклоном назад, обеспечивая уменьшение расстояния между ними и лотком 2 в направлении к копнителю. Консольные брусья заканчиваются расширенными частями (отсекателями), которые препятствуют обратному перемещению соломы из копнителя.
Лоток 2 можно перемещать в вертикальном и горизонтальном направлениях, для чего в боковинах 11 и на корпусе самого лотка имеются пазы под болты крепления.
Соломонабиватель работает следующим образом. Клавиши 1 подводят солому к зоне действия соломонабивателя. Пальцы 3 граблин, опускаясь между консольными брусьями 4, захватывают порции соломы и перемещают их в пространстве между брусьями 4 и лотком 2, где солома подпрессовывается и выбрасывается в копнитель. В начальной стадии камера копнителя заполняется соломой без уплотнения. После заполнения камеры каждая порция соломы, поданная граблинами из зоны подпрессовки, уплотняет всю массу соломы в камере копнителя до определенной плотности.
Половонабиватель 15 предназначен для подачи половы, поступающей к нему с очистки комбайна, на платформенную часть днища 13 копнителя. Он состоит, также как и соломонабиватель, из коленчатого вала (он имеет одно колено), граблины, закрепленной на коленчатом валу с помощью деревянных подшипников, кулисы и противовесов. Под половонабивателем установлен лоток, по которому граблины перемещают полову в копнитель.
Работает половонабиватель также, как и соломонабиватель.
Предохранительная муфта и автомат выгрузки
Привод этих рабочих органов копнителя осуществляется от заднего контрприводного вала 11 с левой стороны комбайна через звездочку 9 (рис.6.) Она жестко соединена с ведомым диском 8 предохранительной муфты. В состав предохранительной муфты входят ведущий диск 4 с кулачком 6 и коническая пружина 1 с центрирующей шайбой 2. Ведущий и ведомые диски свободно посажены на втулку 5. Муфта вместе со звездочкой 9 получают вращательное движение от приводного диска 3, который с помощью шпоночного соединения установлен на контрприводном валу 11. Приводной диск 3 и ведущий диск 4 соединены между собой пальцевым соединением (см. Сечение А-А на рис.6.), А ведущий 4 и ведомый 8 диски муфты имеют зубчатое соединение (см. Вид Б), которое плотно сжато конической пружиной 1.Степень подпрессовки соломы в копнителе ограничивается предохранительной муфтой, которая регулируется на передачу крутящего момента 85...100...Нм путем изменения усилия сжатия конической пружины 1.
При повышении значения этого момента на валах соломонабивателя, муфта отключает на них привод. Это может привести к забиванию соломотряса., так как он продолжает работать. Поэтому предохранительная муфта сблокирована с автоматом выгрузки копны. В действие он приводится кулачком 9 (рис. 7), расположенном на ведущем диске муфты.
Автомат выгрузки состоит из коромысла 5, горизонтальная ось 11 которого закреплена на кронштейне 1 рамы. С помощью оси 6 и болта 13 с пружиной к коромыслу присоединен рычаг 7, с закрепленным на его внешнем конце роликом 8. Внешний конец коромысла 5 через тягу 3 с вилкой 4 соединен с промежуточным рычагом механизма выгрузки копны.
Автомат работает следующим образом. Когда момент сопротивления на валах соломонабивателя превысит значение крутящего момента, на который отрегулирована предохранительная муфта, ведомый диск 8 (рис. 6) муфты со звездочкой 9 останавливаются, а ведущий диск 4, пробуксовывая в зубчатом зацеплении с ведомым диском 8, периодически перемещается вдоль оси контрприводного вала 11. При таких перемещениях ведущего диска боковая грань его кулачка 9 (рис. 7) может войти в соприкосновение с боковой гранью ролика 8 и отклонить рычаг 7 в сторону конической пружины. Как только боковая грань кулачка выходит из соприкосновения с роликом, пружина 14 болта 13 возвращает рычаг 7 в рабочее положение, а ролик 8 устанавливается на беговую дорожку кулачка. При набегании ролика на кулачок рычаг 7 вместе с коромыслом 5 поворачивается вокруг оси 11, отводя тягу 3 вниз, которая включает механизм выгрузки и копнитель разгружается без участия комбайнера.
Технологический процесс работы комбайна
Технологический процесс работы комбайна протекает следующим образом (рис. 8). Хлебная масса, скошенная жаткой 1 или подобранная подборщиком из валков, с платформы жатки поступает в наклонную камеру 2, где плавающим транспортером перемещается к приемному битеру 3. Приемный битер 3 направляет массу к первому молотильному барабану 4, где происходит выделение наиболее спелого, крупного и легко вымолачиваемого зерна, которое частично сепарируется через решетку подбарабанья. Поэтому первый барабан работает с пониженной частотой вращения и с увеличенным зазором между бичами и подбарабаньем.Далее хлебная масса поступает под действие промежуточного битера 5, который направляет ее ко второму барабану. При этом в выключенное первым барабаном зерно из слоя хлебной массы продолжает выделяться через сепарирующую решетку 13 (рис. 1) на транспортную доску грохота 15.
Второй барабан настраивают на большую частоту вращения, а зазоры между бичами барабана и планками подбарабанья устанавливают меньшими, чем в первом. Он осуществляет окончательный обмолот хлебной массы и дальнейшую сепарацию зерна через решетку второго подбарабанья. Солома выбрасывается отбойным битером 7 (рис.8) по направляющей решетке на соломотряс 9, где происходит окончательное выделение зерна из соломы, а солома клавишами соломотряса транспортируется к соломонабивателю копнителя.
Выделенное молотильным устройством и соломотрясом зерно вместе с половой и сбоиной поступает на транспортную доску, где под действием колебательного движения происходит расслоение вороха: зерно и тяжелые примеси опускаются на поверхность транспортной доски, легкие и крупные соломистые примеси всплывают. В таком состоянии ворох поступает на пальцевую решетку воздушно-решетной очистки 11. Крупные примеси, поддерживаемые воздушным потоком, сходят с пальцевой решетки на середину верхнего жалюзийного решета, а зерно с тяжелыми примесями поступает на его начало. Поэтому основная масса зерен и мелких примесей просеиваются в начале верхнего, а затем и нижнего решет. Одновременно воздушным потоком, создаваемым вентилятором, выдуваются все легкие примеси, которые попадают к половонабивателю копнителя.
Чистое зерно попадает на скотное дно нижнего решетного стана и далее в кожух шнека зернового элеватора 12, который транспортирует его в верхний распределительный шнек бункера 6.
Непросеянное сквозь верхнее решето часть вороха поступает на удлинитель, где происходит сепарация необмолоченных колосьев, которые вместе с крупными примесями, сходящими с нижнего решета, попадают в шнек колосового элеватора 10. Необмолоченные колосья доставляются в домолачивающее устройство, состоящее из бильного барабана и гладкого подбарабанья. Продукты домолота шнеком подаются на транспортную доску.
Шнековый транспортер (у обоих элеваторов и в бункере) представляет собой вращающийся в кожухе вал с приваренной по спирали лентой. Нижние шнеки имеют люки для очистки.
Элеватор (колосовой и зерновой) состоит из прямоугольной трубы и цепи со скребками. Скребки захватывают продукты транспортировки (зерно, колосья), подаваемые в нижнюю головку элеватора, и скользя по дну наклонной трубы, перемещают их к месту подачи.
Настройка и регулировки молотилки комбайна
Регулировки молотильного устройства.
Молотильное устройство имеет две регулировки:-
Изменение зазоров между бичами
обоих барабанов и планками их подбарабании;
Изменение частоты вращения обоих барабанов.
Регулировка зазоров в молотильных аппаратах производится при помощи рычагов 2 и 3 (рис.30), расположенных в кабине водителя. Конструкция механизма регулирования позволяет изменять зазоры в пределах 18...50 мм на в ходе и 3...48 мм на выходе молотильных аппаратов.
Исходные зазоры в молотильных аппаратах устанавливают в положение рычагов 2 и 3 на вторых сверху пазах зубчатых секторов. Этому положению рычагов должны соответствовать зазоры на входе 20мм для первого и 18мм для второго барабанов, а на выходе 7мм для первого и 6мм для второго барабанов.
Установку оптимальных зазоров, соответствующих условиям работы, выполняется рычагами 2 и 3, а корректировку осуществляют изменением длины подвесок 14 (их восемь для обоих аппаратов) за счет регулировочных болтов 12 (их тоже восемь).
Величины зазоров должны уменьшаться с увеличением влажности и засоренности посевов, а также при уборке трудно обмолачиваемых культур.
Если возникает необходимость максимально опустить подбарабанья, делают это с помощью стяжных гаек 5 и 15 на тягах механизма перемещения подбарабании.
Для регулирования частоты вращения барабанов молотильное устройство оборудовано гидрофицированными клиноременными вариаторами одинаковой конструкции (рис 9). Вариатор состоит из шкива 1 на валу барабана и шкива 2 на контрприводном валу. На шкивах установлен клиновой ремень 4. Каждый шкив состоит из подвижного и неподвижного дисков, соедин1нных между собой пальцами. Подвижные диски перемещаются в осевом направлении валов с помощью синхронно действующих гидроцилиндров 3 и 8 с подпорными клапанами 6. Управление вариаторами осуществляют из кабины водителя через гидрораспределитель, имеющий запорные клапаны повышенной надёжности и герметичности.
Штоки гидроцилиндров навёрнуты на валы барабана и контрпривода и вращаются вместе с ними. Гильзы гидроцилиндров являются подвижными деталями - они перемещают подвижные диски шкивов. При этом гильза цилиндра на валу барабана передаёт толкающее усилие на подвижный диск, а гильза на контрприводном валу - тянущее усилие через тарелку и стяжные болты. На шкиве вала барабана подвижным диском является пружинный, а на валу контрпривода - внутренний.
При нейтральном положении рукоятки гидрораспределителя подпорные клапаны запирают масло в рабочих полостях гидроцилиндров вариаторов.
Для уменьшения частоты вращения барабана рукоятку гидрораспределителя устанавливают так, чтобы масло от насоса гидросистемы комбайна поступало в подпорный клапан и далее в гидроцилиндр на валу барабана. Гильза этого цилиндра переместит наружный подвижный диск в направлении к неподвижному диску шкива, вследствие чего ремень вытесняется на увеличенный диаметр шкива барабана. Одновременно с этим ремень отодвигает подвижный внутренний диск шкива контрпривода от наружного неподвижного и перемещается на меньший диаметр. В результате этого в гидроцилиндре возрастает давление масла, которое преодолевает усилие сжатия регулировочной пружины в подпорном клапане и поступает в сливную магистраль гидросистемы.
и т.д.................
Отправить свою хорошую работу в базу знаний просто. Используйте форму, расположенную ниже
Студенты, аспиранты, молодые ученые, использующие базу знаний в своей учебе и работе, будут вам очень благодарны.
Размещено на http://www.allbest.ru/
Размещено на http://www.allbest.ru/
Общее устройство и технологический процесс зерноуборочного комбайна
1. Количественные и качественные показатели комбайна
Зерноуборочные комбайны предназначены для уборки зерновых колосовых культур. При оборудовании комбайнов специальными приспособлениями ими убирают кукурузу на зерно, просо, гречиху, рапс, подсолнечник, сою, семенные посевы трав, сахарной свеклы, овощных и лекарственных культур. Уборка этих культур сопровождается выполнением комбайнами следующих технологических процессов: скашивание или подбор стеблей из валков и транспортирование их в уборочной машине; вымолот зерна из колосьев и сепарация его из соломы; очистка зерна от примесей и транспортировка его в бункер; сбор соломы в цельном, измельченном, прессованном виде или разбрасывание ее на поле.
Комбайны бывают прицепные и самоходные. Наиболее распространены самоходные комбайны. По типу молотильно-сепарирующих рабочих органов комбайны делят на две группы: с классической и аксиально-роторной молотилкой. К первой группе относятся самоходные комбайны СК-5М «Нива», «Енисей-1200», «Кедр-1200», «Дон-161», «Дон-1500Б», ко второй -- самоходные комбайны СК-10В «Ротор», «Дон-2600» и прицепной комбайн ПН-100 «Простор».
Рассмотрим устройство и рабочий процесс комбайнов первой группы на примере комбайна «Дон-1500Б».
Размещено на http://www.allbest.ru/
Размещено на http://www.allbest.ru/
Комбайн «Дон-1500Б» (рис. VIII.3) состоит из жатвенной части
А, включающей в себя жатку, проставку Б и наклонную камеру В, молотилки Г, бункера 10, копнителя 18, двигателя 8, трансмиссии, ходовой системы, гидросистемы, кабины 6, органов управления, электрооборудования и электронной системы контроля технологического процесса и состояния агрегатов. На комбайне «Дон-1500» вместо копнителя можно установить универсальное приспособление для измельчения и сбора соломы и половы в прицепные тележки или разбрасывания их по полю.
В фронтально (спереди) присоединена к раме молотилки У. Жатка соединена с проставкой Б шарнирно и может совершать колебательные движения как в продольной, так и в поперечной вертикальной плоскости. Такое соединение жатки с проставкой обеспечивает ей возможность при опоре на поверхность поля башмаками 38 копировать рельеф поля и поддерживать установленную высоту среза растений режущим аппаратом 39.
На жатке смонтированы делители 41, мотовило 1, режущий аппарат 39, шнек 3, копирующие башмаки 38, в проставке Б -- битер 37, а в наклонной камере В -- транспортер 4. Для подбора валков на жатке устанавливают подборщик, мотовило снимают, а режущий аппарат 39 отключают.
В зонах, где преобладает раздельный способ уборки, вместо жатки на комбайн навешивают платформу-подборщик.
Молотилка состоит из следующих основных частей и механизмов: молотильно-сепарирующего устройства (МСУ), включающего в себя барабан 5, подбарабанье 33 и отбойный битер 7, соломотряса 16, транспортной доски 32, очистки, зернового 30 и колосового 28 шнеков, зернового 13 и колосового 75 элеваторов, домолачивающего устройства 9, снабженного распределительным шнеком. Очистка, расположенная под соломотрясом, состоит из верхнего 26, нижнего 27, жалюзийных решет, удлинителя 25 и вентилятора 31. На крышке молотилки установлен бункер 10, снабженный загрузочным 12 и выгрузным 11 шнеками.
Комбайны снабжены пневматическими колесами: передними ведущими 35 и задними управляемыми 24. Все механизмы и ведущие колеса приводятся в действие от двигателя 8. Работой комбайна управляет машинист при помощи гидравлической системы и соответствующих механизмов, расположенных в кабине.
Рабочий процесс комбайна протекает следующим образом.
Пальцы подборщика, смонтированного на жатке, подают стебли из валков на платформу или мотовило 1 и укладывают на нее стебли, срезанные режущим аппаратом 39. Шнек 3 сужает поток стеблей (хлебная масса) и направляет их к битеру 37, а от него -- к плавающему транспортеру 4. Нижняя ветвь транспортера перемещает стебли в молотильный аппарат. Вращающийся барабан 5 наносит удары по потоку хлебной массы, перемещает ее по подбарабанью 33 и обмолачивает.
Обмолоченная хлебная масса (грубый ворох) состоит из соломы, зерна, половы и примесей. Мелкие части грубого вороха, зерно и полову принято называть мелким зерновым ворохом.
Основная часть (70-80 %) зернового вороха в процессе обмолота проходит сквозь отверстия подбарабанья и падает на транспортную доску 32.
Солома с остатками зернового вороха выбрасывается барабаном с большой скоростью. Отбойный битер 7 уменьшает скорость перемещения соломы и направляет ее на соломотряс 16. Во время перемещения массы по пальцевой решетке, установленной под битером 7, происходит дальнейшее выделение зерна из соломы. Битер, непрерывно отводя обмолоченную массу от барабана, предупреждает наматывание на него стеблей.
Ступенчатые клавиши соломотряса 16, совершая круговые движения, интенсивно перетряхивают солому. Зерно и мелкие примеси просыпаются сквозь отверстия клавиш и сходят по их наклонному дну на транспортную доску 32. Гребенки клавиш продвигают солому к выходу из молотилки.
Зерновой ворох, выделенный подбарабаньем и соломотрясом, по транспортной доске 32 ссыпается на верхнее жалюзийное решето 26 очистки. Зерно просыпается сквозь просветы решета и падает на нижнее решето 27. Под решета направлена струя воздуха от вентилятора 31, которая уносит в копнитель 18 легкие примеси (полову). Очищенное зерно, прошедшее сквозь нижнее решето, собирается в желобе шнека 30, подается скребковым транспортером элеватора 13 в шнек 12 и загружается в бункер 10.
В процессе обмолота часть колосков отламывается от стеблей и необмолоченными поступает на очистку. Такие колоски сходят с верхнего решета на его удлинитель 25 и сквозь просветы последнего просыпаются в желоб колосового шнека 28, который их сбрасывает на наклонный транспортер (элеватор) 15, направляющий колоски в домолачивающее устройство 9. Вращающийся ротор устройства во взаимодействии с зубчатым подбарабанье обмолачивает колоски и сбрасывает образовавшийся ворох в кожух шнека, который подает ворох на транспортную доску 32 по всей ее ширине. В дальнейшем этот ворох поступает на решето 26 очистки для выделения из него зерна.
Крупные примеси (сбоина), не прошедшие сквозь просветы удлинителя, вместе с легкими примесями (половой) выводятся из молотилки. Из бункера зерно выгружают шнеком 11 на ходу или на остановках.
Для сбора соломы и половы на комбайн навешивают гидрофицированный копнитель 18 или измельчитель. В копнитель солома подается соломонабивателем 77, а полова -- половонабивателем 23. Сформированная копна выбрасывается на поле. Комбайн, снабженный измельчителем, может собирать измельченную солому вместе с половой в прицепленную сзади тележку, укладывать солому в валок или разбрасывать по полю.
Устройство и принцип работы остальных комбайнов первой группы в основном аналогичны. Различаются они размерами, устройством отдельных агрегатов, пропускной способностью и производительностью.
Комбайн «Дон-161» предназначен для уборки высокоурожайных посевов зерновых и других культур. Комбайн имеет усовершенствованную молотильно-сепарирующую систему, увеличенную площадь решет очистки и вместимость бункера. Комбайн может комплектоваться жатками четырех типоразмеров и платформами-подборщиками двух типоразмеров. Комбайн снабжают измельчителем или капотом для укладки соломы в валок.
Зерноуборочный комбайн «Енисей-1200» снабжен двухбарабанным молотильно-сепарирующим устройством. Его применяют для уборки зерновых в условиях повышенной влажности хлебной массы. Выпускается три модификации этого комбайна: «Енисей- 1200-1» с однобарабанным молотильным аппаратом для уборки зерновых в зонах с пониженным увлажнением; «Енисей-1200Н» для уборки влажных длинносоломистых и полеглых хлебов в условиях нечерноземной зоны; гусеничная модификация «Енисей-1200Р» с передним штифтовым барабаном для уборки риса.
Зерноуборочный комбайн «Кедр-1200» снабжен однобарабанным молотильно-сепарирующим устройством, а его модификации «Кедр-1200Н» и «Кедр-1200Р» -- двухбарабанным. У комбайна «Кедр- 1200Р» первый молотильный барабан -- штифтовый, а у «Кедр-1200Н» --бильный. Базовая модель «Кедр-1200» предназначена для уборки хлебов в условиях нормальной влажности;
модификация «Кедр-1200Н», имеющая повышенную проходимость, -- для уборки влажных длинносоломистых и полеглых хлебов в условиях Нечерноземной зоны; гусеничная модель «Кедр- 1200Р» --для уборки риса.
Зерноуборочный комбайн «Дон-091», снабженный днобарабанным молотильно-сепарирующим устройством, предназначен для уборки зерновых и других культур в условиях нормальной и повышенной влажности. Устройство и принцип работы зерноуборочных комбайнов второй группы рассмотрим на примере комбайна СК-10.
Комбайн СК-10 (рис. VIII.4), предназначенный для уборки высокоурожайных хлебов, отличается от комбайна «Дон-1500» устройством молотилки. В молотилке СК-10 применено принципиально новое аксиально-роторное молотильно-сепарирующее устройство, в котором вымолот, сепарацию зерна и перемещение хлебной массы к выходу выполняет вращающийся ротор 24. Ось его вращения расположена вдоль продольной оси молотилки.
Ротор состоит из приемной А, молотильной Б и сепарирующей В частей, различающихся конструкцией активных элементов, которыми ротор воздействует на поток стеблей.
Приемная часть ротора снабжена тремя винтообразными лопастями 26 и заключена в конический кожух 25. Части Б и В ротора заключены в цилиндрический кожух, составленный из обмолачивающей деки 23, сепарирующих решеток 9, винтовых направляющих, установленных по всей длине кожуха, входного и выходного окон.
Размещено на http://www.allbest.ru/
Размещено на http://www.allbest.ru/
Хлебная масса подается транспортером 4 в приемную часть А ротора 24, захватывается лопастями 26 и подается к бичам 22, которые, ударяя по колоскам, вымолачивают зерно и увлекают массу во вращение. Масса, ударяясь о винтовые направляющие, перемещается по винтовой траектории от входа к выходу. Зерно и мелкие примеси проходят через отверстия решетчатой деки 23 и решеток 9 в шнеки 21 и подаются на верхнее решето 17 очистки. Рабочий процесс очистки аналогичен рабочему процессу очистки комбайна «Дон-1500».
Очищенное зерно поступает в шнек 19, из него в элеватор 8 и загружается в бункер 6. Солому, выходящую из кожуха ротора, захватывает битер 10 и подает в измельчитель 14. Полова, сходящая с удлинителя 75 очистки, поступает в шнек измельчителя 14, из него в кожух вентилятора и далее вместе с соломой загружается в прицепленную к комбайну тележку.
Комбайн может укладывать солому с половой в валок или разбрасывать их по полю.
Комбайн «Дон-2600» снабжен аксиально-роторным молотиль- но-сепарирующим устройством. Он отличается от комбайна СК- 10 конструкцией привода ротора, очистки и устройства для сбора мелкого зернового вороха и подачи его на очистку. «Дон-2600» снабжен дополнительным транспортером для подачи соломы в копнитель. На место снятого копнителя можно навешивать измельчитель и капот для укладки соломы в валок.
Прицепной комбайн ПН-100 «Простор» предназначен для уборки зерновых и других культур на мелкоконтурных участках. Его агрегатируют с тракторами тягового класса 1, 4 и 2. Комбайн снабжен аксиально-роторным молотильно-сепарирующим устройством, ось которого расположена поперек направления движения комбайна параллельно режущему аппарату.
Диаметр ротора 570 мм, длина 1870 мм. Хлебная масса транспортером наклонной камеры подается тангенциально (поперек оси барабана) по касательной к поверхности барабана. В отличие от комбайна СК-10 хлебная масса в комбайне ПН-100 меньше деформируется, а дробление зерна и удельный расход энергии снижены. Комбайн укладывает солому в валок, а сверху на него - полову.
Качество работы комбайнов оценивают по уровню потерь зерна за жаткой и молотилкой, чистоте и дроблению зерна, собранного в бункер. Качество зависит от многих факторов: технического уровня реализованных в комбайне конструктивных решений, состояния и правильной регулировки рабочих органов жатки и молотилки, подачи хлебной массы, ее состава и состояния, засоренности и полеглости посевов, выровненное поверхности и рельефа поля, выбранного направления и скорости движения, мастерства и технологической дисциплинированности комбайнера. Технический уровень комбайна оценивают по показателям, значения которых приведены в таблице VIII. 1.
Размещено на http://www.allbest.ru/
Размещено на http://www.allbest.ru/
Пропускная способность (кг/с) молотилки -- это предельное количество хлебной массы, которую может обработать комбайн за 1 с с соблюдением агротехнических требований.
Номинальную пропускную способность определяют при испытании комбайнов на уборке прямостоячей безостой пшеницы, имеющей длину стеблей 0,7-0,9 м, урожайность не менее 4т/га, влажность зерна и соломы 15-18%, отношение массы зерна к массе соломы 1:1,5, засоренность в зоне среза не более 5 % и массу 1000 зерен более 40 г.
Производительность комбайнов определяют по намолоту зерна (т/ч) или площади пашни, убранной за 1 ч. Номинальная производительность комбайнов по намолоту, указанная в таблице VIII. 1, определена при испытании в тех же условиях, что и номинальная пропускная способность.
Качество функционирования зерноуборочных комбайнов может рассматриваться как с технической, так и с технологической точек зрения. К показателям качества функционирования зерноуборочных комбайнов с технической точки зрения могут быть отнесены, например, показатели их надежности (безотказности, долговечности, ремонтопригодности и сохраняемости), а с технологической точки зрения -- потери зерна (прямые и косвенные). В обоих случаях для оценки качества функционирования зерноуборочных комбайнов необходимо определить степень соответствия исследуемых показателей требованиям потребителя. Эти требования закладываются в конструкцию при проведении НИР и ОКР, обеспечиваются в процессе производства и проявляются при эксплуатации. На рисунке 1 представлена общая схема формирования номинала качества функционирования зерноуборочного комбайна с технической точки зрения. Все нормативы, регламентирующие качество эксплуатации зерноуборочного комбайна, устанавливаются для стандартных (базовых) условий и корректируются для других. В связи с этим номинал качества с технической точки зрения достигается при различной наработке зерноуборочного комбайна, причем при высоком качестве технического обслуживания и ремонта, а также хороших условиях функционирования он достигается с большей наработкой.
Обзор научной литературы и опыт исследований показали, что оценку качества функционирования зерноуборочных комбайнов целесообразно вести на 3 методологических уровнях (рис. 2):
лабораторном, хозяйственном и региональном. Первый методологический уровень охватывает методы и приемы исследований зерноуборочных комбайнов и его систем. На этом уровне учитывают конструктивные параметры машины, их взаимное расположение, характеристики материалов и т.п. Влияние окружающей среды на результаты исследований не учитываются. Этот уровень является элементарным. Теоретические предпосылки на данном уровне основательно разработаны в теоретических курсах сопротивления материалов, теоретической механике, деталях машин и т.д., имеется большой объем экспериментального материала.
Первый методологический уровень нами назван «лабораторным». Но это не означает, что все исследования на данном уровне должны проводиться в лабораторных условиях. Например, исследования прямых потерь зерна зерноуборочным комбайном проводятся в полевых условиях. Объектом исследования на первом уровне является отдельно взятый зерноуборочный комбайн или его системы. По результатам исследований качества зерноуборочного комбайна на первом уровне могут быть рекомендованы изменения конструкции или материала, из которого изготовлена определенная деталь, что приведет к изменениям свойств машины, влияющих на показатели ее качества в процессе эксплуатации. На первом уровне можно прогнозировать или теоретически оценить показатели качества зерноуборочного комбайна, как правило, технические.
Объектами исследования на втором методологическом уровне в зависимости от цели и задач исследования являются процесс уборки зерновых культур или зерноуборочный комбайн, используемый в определенных хозяйственных условиях. Обычно цель уборки, форма и технология четко определены. Установлены относительно стабильные связи между элементами системы, число которых невелико. На данном методологическом уровне при оценке качества функционирования зерноуборочных комбайнов используются достаточно постоянные характеристики внешней среды и их можно учесть в теоретических предпосылках. Управление процессом осуществляют несколько человек, имеющих одну и ту же цель. В службах технического обслуживания и ремонта, бытового и культурного обслуживания, на комбайнах и транспортных средствах работающие имеют, соответственно, практически одинаковую профессиональную подготовку и социально-экономические стимулы. Из этого следует, что научные работы второго методологического уровня не учитывают человеческий фактор. Имеется много научных исследований по качеству работы и надежности зерноуборочных комбайнов для конкретных условий эксплуатации с применением, в основном, теории математической статистики. Так как оценка качества функционирования зерноуборочных комбайнов на втором методологическом уровне осуществляется в условиях конкретного хозяйства, то данный уровень назван «хозяйственным».
На третьем методологическом уровне предполагается проведение исследований в условиях одного зернопроизводящего региона страны (области, края или республики), в состав которого входит определенное множество хозяйств. Управление хозяйствами, как правило, различно, во многих случаях отличаются почвенно-климатические и другие условия, а также социально-экономические стимулы. Применение той или иной технологии, формы уборки зависит от лица, принимающего решение. Процесс исследования на данном уровне имеет сложную иерархическую систему, состоящую из подсистем -- систем второго уровня. Связи между подсистемами нестабильны. Учет факторов третьего уровня весьма сложен.
В связи с этим на данном этапе особая роль отводится методам математической теории исследования операций с выдвижением гипотез изменения показателей качества функционирования зерноуборочных комбайнов в зависимости от субъективных факторов лица, принимающего решение. Объект исследования тот же, что и на втором уровне. На этом уровне необходимо определить показатели качества функционирования зерноуборочных комбайнов в большинстве зерносеющих регионах страны. Третий уровень назван «региональным». Из сказанного выше следует, что основным и наиболее важным для исследования качества функционирования зерноуборочных комбайнов является «региональный» уровень, учитывающий машину, человека и среду. Это уровень обеспечивает системный подход к анализу и оценке показателей качества функционирования зерноуборочных комбайнов. Проведение работ на «региональном» методологическом уровне включает: обоснование и выбор региона, в котором будут проводиться исследования, оценку возможности получения достоверной и полной информации, выдвижение гипотез о влиянии на качество функционировании зерноуборочных комбайнов поведения лица, принимающего решение, установление ограничений на предполагаемые факторы, от которых зависят рассматриваемые показатели качества, выбор показателей качества функционирования зерноуборочных комбайнов, обоснование функции реального результата желаемому (требуемому), выбор методики исследования, сбор информации, моделирование, расчет и выявление эффектов от выбранных факторов, оценка показателей качества функционирования зерноуборочных комбайнов, сравнение показателей качества функционирования зерноуборочных комбайнов с желаемыми (требуемыми).
Следующий этап методологии оценки качества функционирования зерноуборочных комбайнов -- моделирование рассматриваемого процесса. Моделирование, как правило, включает два этапа: разработка (создание) модели (математической или физической); анализ на модели (математическое моделирование или экспериментирование) . Причем, на обоих этапах возможно уточнение модели. По результатам моделирования принимается решение по совершенствованию процесса уборки зерновых культур или конструкции зерноуборочного комбайна в соответствии со следующей структурной схемой (рис. 3).
Показатели качества функционирования зерноуборочных комбайнов проявляются по результатам его работы в условиях реальной эксплуатации.
В связи с тем, что при принятии решения по совершенствованию процесса уборки зерновых культур или конструкции зерноуборочного комбайна учитывается совокупность факторов машины, среды и человека, влияющих на качество функционирования зерноуборочных комбайнов, то для получения значений факторов всех трех групп необходимо иметь информационные источники. Информационными источниками могут быть статистические материалы деятельности сельскохозяйственных предприятий и зерносеющих регионов в целом, данные метеорологических и других служб, результаты сплошного и выборочного хронометража работы зерноуборочных комбайнов и экспериментальных исследований. При этом можно использовать различные методы определения показателей качества: измерительные, регистрационные, органолептические, расчетные, экспертные, статистические. Анализируя возможные информационные данные, можно отметить, что перед началом уборки зерновых культур часть из них известна. К таким можно отнести: урожайность зерновой культуры, соотношение массы зерна к массе соломы, влажность зерна и соломы, засоренность, соотношение посевных площадей под различные зерновые культуры и их сорта, марки зерноуборочных комбайнов, используемых на уборке, и срок их службы и др. Другая часть информационных данных -- неопределенные. Эти данные могут быть случайными с известным или неизвестным распределением, или не стохастической природы.
Список использованной литературы
комбайн уборочный механизм
1. Надежность и эффективность в технике: справочник: в 10 т. / Ред. совет:В.С. Абдуевский (пред.) и др. Т. 7. Качество и надежность в производстве / под общ. ред. И.В. Апполонова. -- М.: Машиностроение, 1989. -- 280 с.
2. Надежность и эффективность в технике: справочник: в 10 т. / Ред. совет:
В.С. Абдуевский (пред.) и др. Т. 3. Эффективность технических систем / под общ. ред. В.Ф. Уткина, Ю.В. Крючкова.-- М.: Машиностроение, 1986. -- 328с.
3. Халанский В.М., Горбачев И.В. «Сельскохозяйственные машины.» -- М.: КолосС, 2004.-- 624 с: ил. -- (Учебники и учеб. пособия для студентов высш. учеб. заведений). ISBN 5-9532-0029-3.
Размещено на Allbest.ru
Подобные документы
Расчёт основных рабочих органов зерноуборочного комбайна, разработка схем работы его элементов: мотовила, режущего аппарата, соломотряса. Анализ факторов влияющих на работу основных рабочих органов зерноуборочного комбайна и оценка их работоспособности.
курсовая работа , добавлен 28.04.2011
Чизельные орудия: общее устройство, особенности конструкции и принципы работы. Машины для почвозащитной системы земледелия и основные приемы защиты почв. Общее устройство и рабочий процесс комбайна ЛК-1. Схема рабочего процесса пресс-подборщиков.
контрольная работа , добавлен 26.12.2012
Общие сведения о способах уборки зерновых. Устройство комбайна и отдельных его частей: молотилки, соломотряса, системы очистки, гидрофицированного копнителя, соломонабивателя; регулировка и настройка их механизмов. Технологический процесс работы комбайна.
реферат , добавлен 18.07.2010
Классификация уборочных технологий. Средства и виды механизации для уборочных работ. Технологический процесс работы уборочных машин. Технико-экономические показатели зерноуборочных комбайнов. Работа зерноуборочного комбайна с очесывающей жаткой.
презентация , добавлен 07.03.2015
Общее устройство гусеничного трактора и назначение его основных частей. Влияние использования тяговой мощности на производительность машинно-тракторного агрегата и себестоимость тракторных работ. Устройство и технологический процесс туковых сеялок.
контрольная работа , добавлен 07.01.2011
Агротехническая оценка зерноуборочного комбайна, определение агротехнических показателей при лабораторно-полевых испытаниях. Энергетическая и эксплуатационно-технологическая оценка комбайна, оценка безопасности и эргономичности конструкции, надежности.
реферат , добавлен 24.04.2014
Агротехнические требования, предъявляемые к зерноуборочным машинам. Оптимизация энергозатрат процесса измельчения зернового сырья путем совершенствования конструкций рабочих органов. Технические характеристики модернизированной конструкции комбайна.
дипломная работа , добавлен 11.07.2016
Обоснование выбора сельскохозяйственной машины. Технический процесс работы комбайна "Енисей-1200", его подготовка к работе, ремонт опорного катка каретки ходовой части. Основные технологические регулировки рабочих узлов, агротехнические требования.
контрольная работа , добавлен 13.10.2015
Краткий обзор и характеристика комбайна кормоуборочного полунавесного КПК-4500 "Полесье". Комплексный расчет экономических показателей использования сельскохозяйственной техники. Определение итоговых показателей экономической оценки эксплуатации комбайна.
курсовая работа , добавлен 04.10.2012
Характеристика видов отвальной вспашки и особенности технологического процесса. Классификация, конструкция и принцип работы плугов. Колесно-пальцевые грабли и их рабочие органы. Устройство и регулировка молотильного аппарата комбайна "Енисей-1200".